我们先来讲一下线切割在稳定的情况下加工时怎么的-钼丝与工件相近运动,直到间隙被电离击穿,火花放电会在极端效应和热熔效应的作用下形成腐蚀,冷却液的爆炸和清洗,使腐蚀迅速排出,新的或高介电系数冷却液使间隙电离恢复绝缘,间隙扩大,钼丝与工件相似。
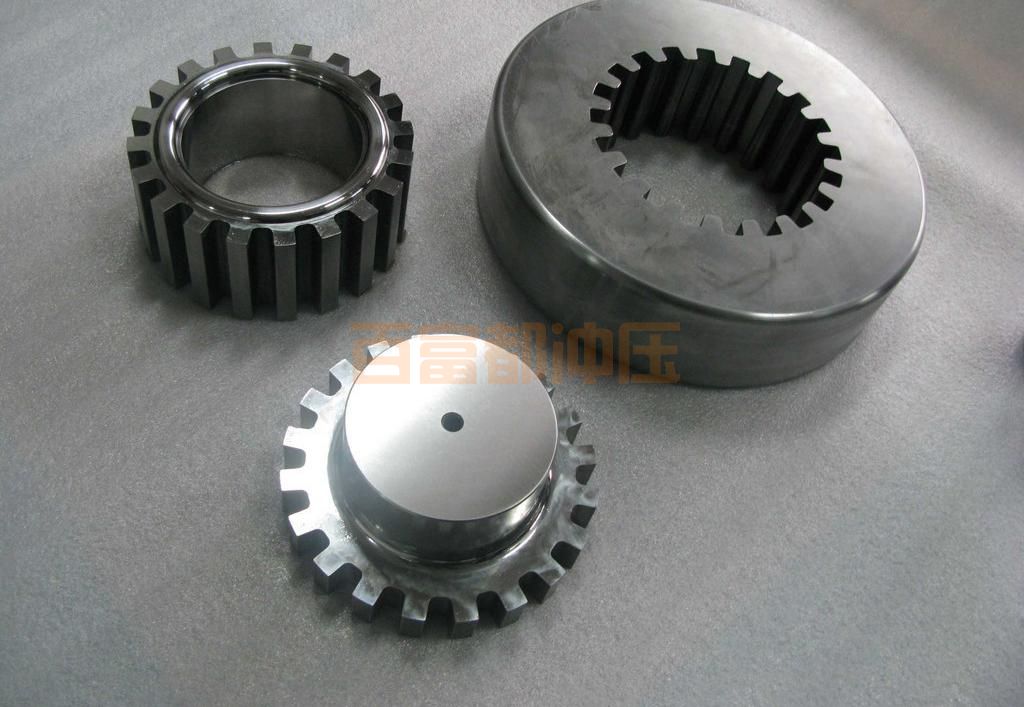
如果上述过程中的任何因素,都会导致加工不稳定。总结后,现问题和解决方案如下:
1、被切割的工件厚度,蚀除五排出路程较长,水进入困难。割高件尽量用水基线切割液,水基线切割液的去屑能力要明显比油基线切割液强,冲洗效果比较好,而割件相对油基液来说也快得多。朋友可以去试试三得利自己生产的亮洁水基线切割液效果到底怎么样。
2、材料杂质,以致取样和间隙跟踪失灵失准,此种情况一般是铸铁件剪切工作常遇到的问题。
3、水爆炸、清洗、电离消除能力差,活性成分少。主要是线切割工作液使用时间长,工作成分消耗过多,建议及时补充或更换新液。
4、运丝速度和轨迹不稳定,间隙混乱。检查线路是否抖动,检查轴承。
5、材料应力变形,局部弹性大,切割缝的细微变形吃掉了放电间隙。最好在切割前静置工件原料,释放内部应力。
6、变频跟踪松紧不适,远离取样电压和变频速度的线性区域。变频必须调整。
7、坐标运动的阻滞和推力的积累(爬行)使放电间隙不确定,跟踪失实不准确。
8、进电阻抗大或接触不良,取样不稳定或远离放电点。直到间隙识别错误。