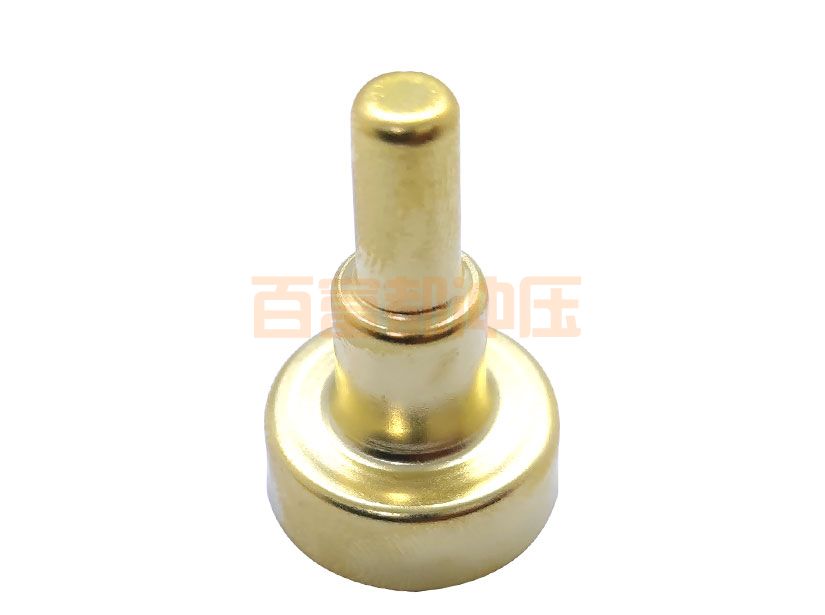
金属冲压件是金属加工件的一种,是可以通过冲压、弯曲、拉伸等方法加工的金属零件。冲压是一种应用非常广泛的金属加工技术,具有高效率和大规模批量生产的特点。根据应用领域的不同,冲压件可分为汽车冲压件、电子冲压件、医疗冲压件等。以下是百富都精密冲压件,里面将介绍冲压模具的冲压工艺:
一般来说,冲压件厂的基本设备包括剪板机、数控冲床/激光、等离子、水射流切割机、折弯机和开卷机、校平机、去毛刺机、点焊机等辅助设备。
一般来说,在冲压模具厂,三个非常重要的步骤是切割,冲孔和折叠。
冲压件有时也称为扳手金属。通常情况下,金属板通过手工或用模具压缩成型进行塑性变形,以形成所需的形状和尺寸,它可以进一步焊接或轻度加工。比较复杂的零件,如烟囱、锡炉、常用的汽车外壳等,都是钣金零件。
冲压件加工称为钣金加工。例如,用木板制作烟囱、铁桶、油罐和平底锅、通风管道等。主要工序有剪切、冲弯、弯曲、焊接、铆接等,需要一定的几何知识。现代钣金工艺包括:激光切割、金属粘接、金属拉丝、等离子切割、轧制、钣金弯曲、模锻、水射流切割、精密焊接等。