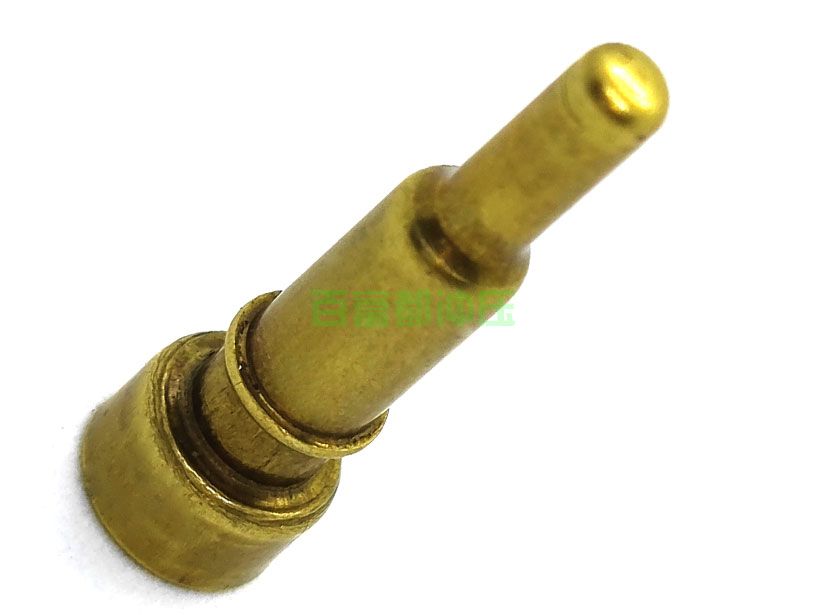
钣金加工是一种常见的金属加工方法,而切削加工是其中的重要组成部分。进行钣金加工时,必须掌握一些切削技巧,以保证加工质量和效率。下面介绍几种常用的钣金加工切割技术:
手工切割:手工切割是一种传统的钣金加工方法,适用于小零件的生产。其优点是灵活、易学,但缺点是精度低、效率低。手工切割需要使用锯或刀片等工具来完成手工切割。
数控切割:数控切割是一种高精度、高效率的钣金加工方法。它采用计算机控制系统控制机床的运动,实现对金属材料的精确切削。数控切割适用于大型零件和复杂形状的加工,可大大提高生产效率和产品质量。
激光切割:激光切割是一种高效、高精度的钣金加工方法。它利用激光束对金属材料进行加热和切割,具有非接触、无振动等优点。激光切割适用于薄板材料的加工,可实现高精度、高效率的切割。
冲裁:冲床切割是一种切割分离金属材料的方法。适用于各种形状、尺寸零件的生产,可实现高速、高效生产。冲压切割需要使用模具和压力机等设备,这样可以实现高精度、高质量的切割。
总之,不同的钣金加工切割技术适用于不同的场合和材料。择合适的切割方式,可以提高加工效率和产品质量,减少成本和浪费。因此在进行钣金加工时,要根据具体情况选择合适的切割方法,并严格遵守安全操作规程,确保人员和设备的安全。