Author gangguan
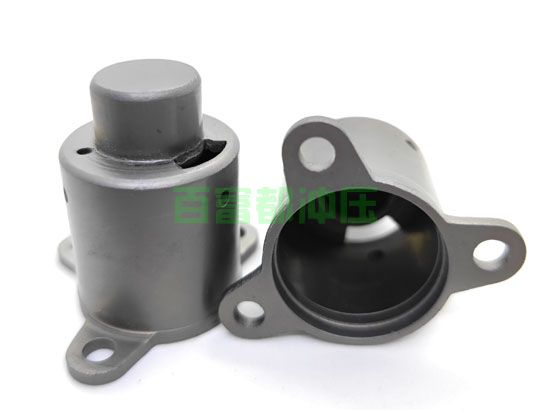
金属冲压件加工厂加工的金属冲压件有着广泛的应用,包括汽车行业。属于汽车冲压件的金属冲压件有很多种类,那么汽车冲压件有哪些呢?下面就带大家来了解一下。
构成汽车零部件的金属冲压件都是汽车冲压件。在汽车的冲压件中,有一部分冲压后直接成为汽车零部件,另一部分需要经过焊接、机加工、或喷漆,才能在冲压后成为汽车零部件。
汽车冲压件的种类很多,如汽车减震器冲压件弹簧托盘、弹簧座、弹簧支架、端盖、盖、压缩阀盖、压缩阀套、油封座、底盖、防尘盖、叶轮、油桶、吊耳、支架等。均属于汽车冲压件。
汽车冲压件生产中大量采用冷冲压工艺,适应了汽车冲压件行业多品种、大批量生产的需要。
在中重型汽车中,大部分覆盖件如车身外板,以及一些承载和支撑件如车架、车厢等汽车零部件都属于汽车冲压件。冷冲压用钢主要是钢板和钢带,占整车用钢量的72.6%。
冷冲压材料与汽车冲压件的生产密切相关。料的好坏不仅决定产品的性能,而且直接影响汽车冲压件工艺的工艺设计,影响产品的质量、成本、使用寿命和生产组织。因此,合理选择材料是一项重要而复杂的任务。
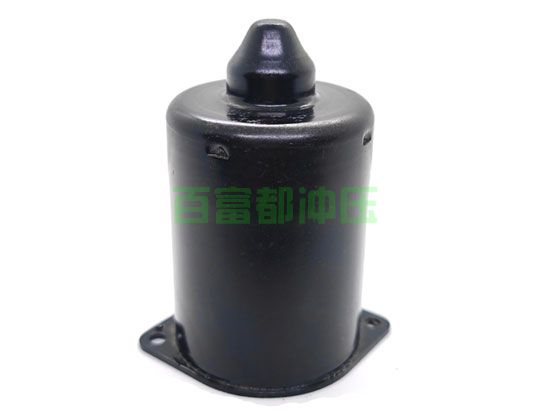
五金冲压件生产厂家在拉深圆柱形金属冲压件时,当拉深高度较大时,由于冲床的工作行程较大,可能会出现压力机压力充足但功率不够的现象。此时应计算拉丝功率,检查压力机电机功率。下面将介绍拉深工作的计算公式和压力机电机功率的计算公式。
- 绘图工作的计算公式如下:W=C最大频率h/1000
在公式中,W–绘图工作,J。
最大拉伸力(包括压入力),N。
H-冲头的工作行程,mm。
系数与拉伸力曲线有关,C值可在0.6~0.8之间。 - 压机的电动机功率可按下式计算:Pw=千瓦n/(60×1000×η1η2)
电动机功率,千瓦
克不平衡系数K=1.2~1.4
拉深工作,J。
不印刷机每分钟的笔画数。
压力机的效率,η1=0.6~0.8
η2=电机效率,η2=0.9~0.95。
如果所选压力机的电机功率小于计算值,则应选择另一个规格更大的压力机。
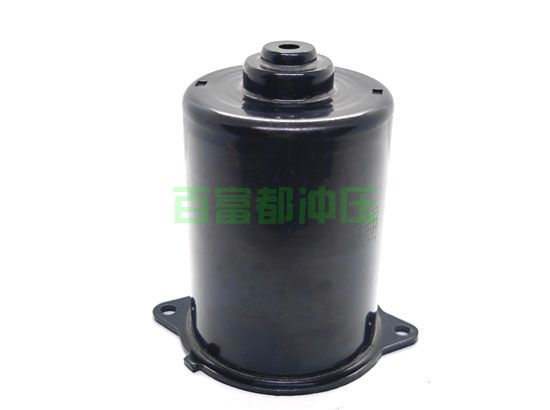
我们的五金冲压件加工厂可以加工汽车的常规五金冲压件,也可以为汽车零部件厂家加工小型钣金冲压件。我今天在这里不谈金属冲压件。编辑今天就给大家介绍一下汽车钣金冲压件的相关知识——即汽车钣金冲压件的材质有哪些要求,下面和大家分享一下吧。
- 价格低廉,经济实用
车的任何部件,都要在满足工况条件的情况下考虑经济性。可以用黑色金属代替有色金属。能用有色金属,绝不能用贵金属。汽车钣金件的寿命应与其他汽车零部件的寿命相适应。 - 钣金材料必须具有良好的塑性
必须具有在外力作用下产生永久变形而不受损伤的能力。对于冷作件,要求有良好的冷塑性,如汽车零部件的冲压件。对于热作零件,则必须具有良好的热塑性,如热锻弹簧钢板、热铆铆钉等。 - 良好的可焊性
许多汽车钣金件是采用点焊、氧焊、电弧焊或气体保护焊等方法焊接在一起的,因此钣金件必须具有良好的焊接性能。这一点在汽车维修和保养中尤为重要,因为焊接性好的材料焊接强度高,开裂倾向低。 - 良好的尺寸精度和板的内在质量
钣金件的尺寸精度和内在质量影响钣金加工。影响很大,尤其是模塑件。 - 化学稳定性好
汽车覆盖件大多在露天工作,经常与水和蒸汽接触,特别是像消声器,经常在较高的温度和腐蚀性气体中工作。这就要求钣金件必须具有良好的化学稳定性,即要求在常温下具有耐腐蚀性和较强的防锈性,并要求在高温或阳光暴晒下不腐蚀、不变形。
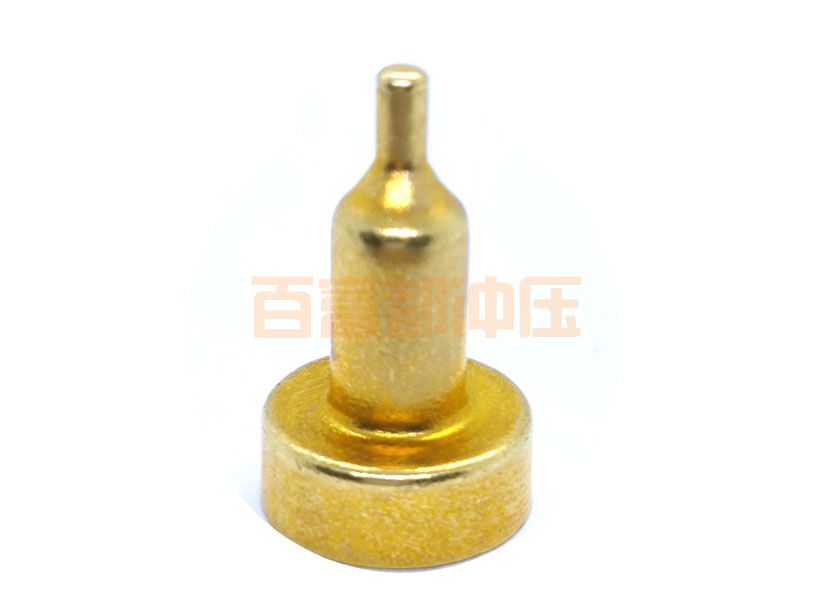
电子冲压件在汽车AB系统中是不可缺少的,为什么这么说。看看这辆车的ABS系统的组成就知道了。
汽车ABS系统主要由传感器、电子控制装置和执行器三部分组成。浙江百富都精密冲压有限公司为汽车制动器公司提供ABS系统的电子冲压件。这类冲压件属于汽车冲压件中的一般冲压件。
ABS是汽车防抱死制动系统的简称。ABS系统又称电控防抱死制动系统。ABS的功能是防止车辆紧急制动时车轮不转动和锁定。为什么要防止车轮锁死?因为车轮与地面在正常情况下是滚动摩擦的,在滚动状态下,我们可以控制车辆的行驶方向。但如果刹车时车轮抱死,那么车轮就从滚动摩擦变为滑动摩擦,这样我们就失去了对车辆方向的控制,如果前方有任何障碍物,我们也无法逃脱。ABS的作用是让汽车在遇到紧急停车时达到最短的制动距离,并且在整个过程中不会有滑动摩擦,保证汽车行驶更加平稳。
ABS系统的原理是利用四个车轮的速度传感器来感知车轮,很多已经刹车的车轮被锁定并旋转,传感器会向计算机发送信号,计算机可以减少锁定车轮上的制动力,使车轮恢复旋转,制动力将使车轮恢复旋转,车轮将再次被锁定。在循环的影响下,车轮会在点制动状态下制动,从而可以达到每秒13次以上,这样就可以将最大的制动力用于制动,而不会出现车轮抱死和侧翻,失控的情况,所以现在ABS已经成为汽车的标准被动安全配置。
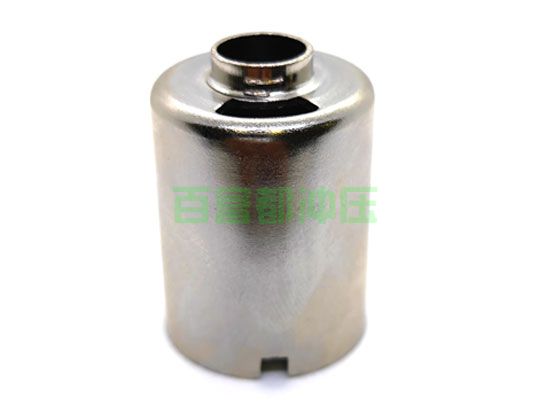
翻边是金属冲压件的一种成形工艺。翻边按变形性能可分为伸长翻边和压缩翻边。让我们了解这两种翻边是如何进行的,以及翻边时应注意什么。
- 沿凹非封闭曲线的细长形翻边的平面或曲面翻边就属于这类翻边。它们的共同特点是坯料变形区在切向拉应力的作用下主要产生切向伸长变形,因此这类冲压件的边缘容易产生裂纹。
1) 细长形平面翻边的变形与车削孔相似。由于翻边过程中应力变形区分布不均匀,翻边后零件的垂直边高往往两端偏高,中间偏低。为了获得平坦的翻边高度,在翻边前应对毛坯的两条轮廓线进行修正。如果翻边高度不大,则不需要校正。
2)对细长曲面进行翻边时,坯料底部中间位置易产生起皱,设计模具时应采用强力压紧装置防止。此外,为翻边创造有利条件,防止中间部分过早翻边,使垂直边伸长率过大、变形甚至开裂。模具表面应进行校正。同时,冲压方向的选择应保证翻边力在水平方向上的平衡。通常情况下,冲压方向与毛坯两端切线所形成的角度是相同的。 - 沿凸不闭曲线进行平面或曲面翻边的压缩翻边属于压缩翻边。变形特点是毛坯变形区主要受切向压应力的影响,因此工件在成形过程中容易起皱。
1)压缩式平板翻边变形与拉深相似。由于翻边时垂直边缘上的应力分布不均匀,翻边后零件垂直边缘的高度会出现中间高、两端低的情况。为了获得平齐的垂直边,毛坯的扩大形状应加以修改。翻边量不大时,不需要校正。另外,当翻边高度较大时,模具应设计有压紧装置,以防止起皱。
2) 压缩型曲面翻边的主要问题是变形区的失稳和起皱。为了防止起皱,应将模具矫正成一定的形状。冲压方向的选择原则与拉长法兰的选择原则是一致的。
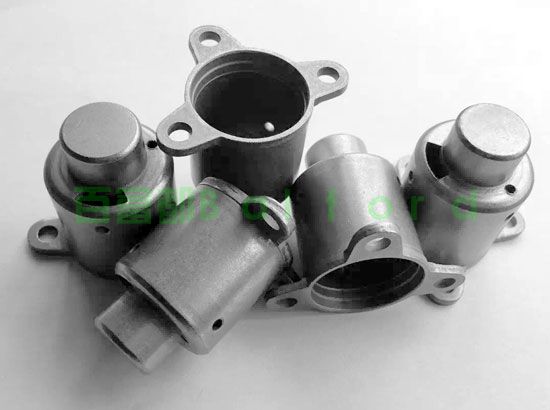
五金冲压模具的调试与制造有什么关系?
在五金冲压件厂,装配好的模具送去调试工序时,检验人员必须按图纸的设计要求对模具进行初步检验,必须有一套完整的模具图纸、工艺卡,并在制造过程中留有样品和样件。初步检验合格后,方可进行下一次调试工作。
调试过程中,如发现模具零件与设计要求不一致,应退回钳工处进行修理。模具的定位零件应按图纸要求进行装配,但当图纸上不能给出尺寸时,可在调整过程中根据具体情况进行定位。按图纸规定调试后需要淬火的零件,如弯曲、拉深、成形凸模和凹模,模具制作者应先做出非常相似的形状,并做好螺孔和销孔。工一起调整校正,直至冲裁出合格的产品零件,确定尺寸和形状,然后进行淬火处理。
由此可见,五金冲压模具零件的完成和装配并不意味着模具的完成。模具在调试过程中必须不断地修正和改进,直到模具能批量生产出合格的冲压件,并能交付使用。生产的正常使用才是真正的制造完成。
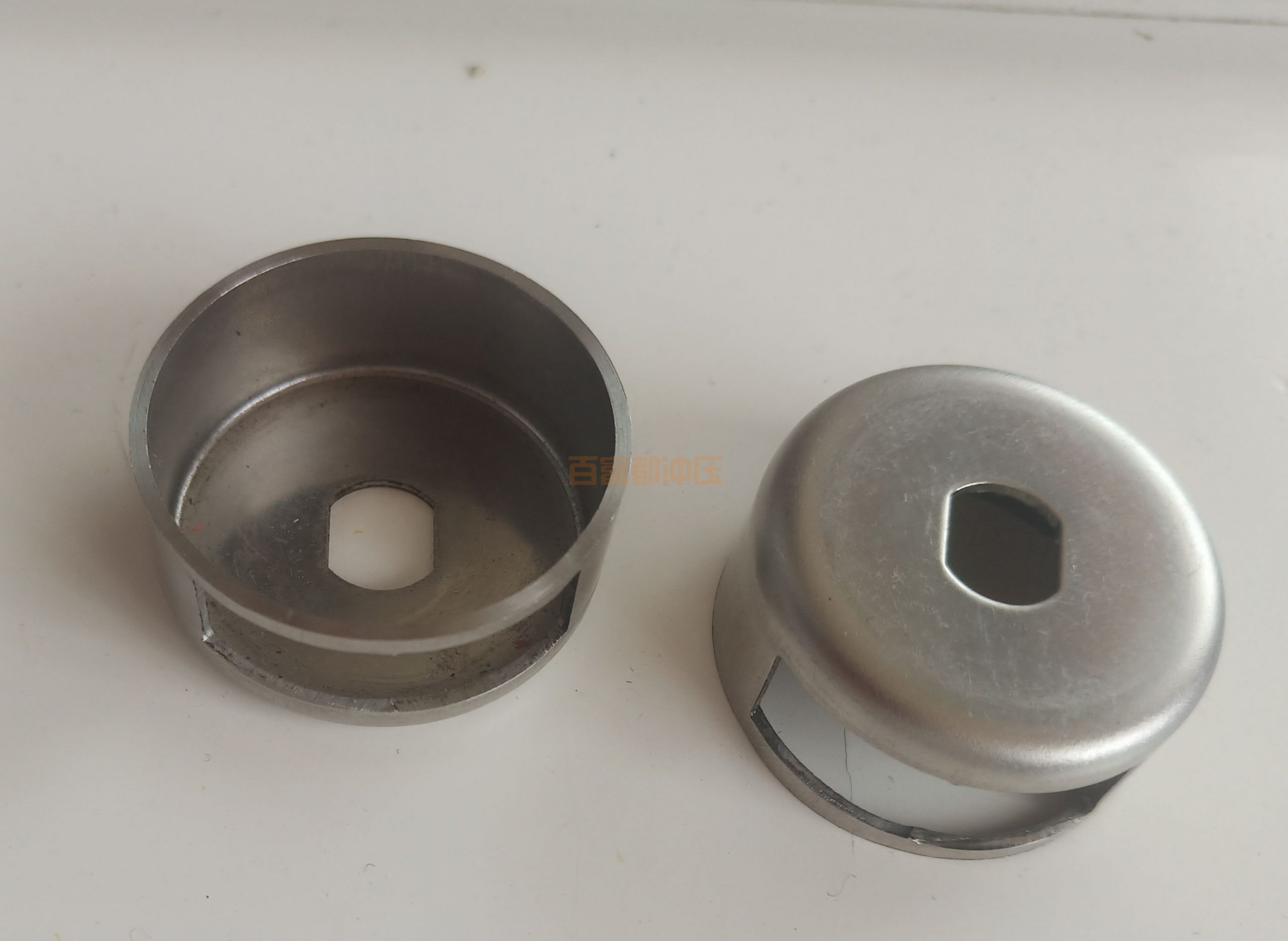
对五金冲压件的质量要求。
在冲压件厂,对五金冲压件的加工质量的要求是非常严格的。因此,要严格控制冲压件的形状和尺寸:首先,对弯曲件的要求:。
- 弯曲件的形状应尽量对称,弯曲半径应不小于材料允许的最小弯曲半径。
- 曲边过短,不易形成,故曲边的直部应H>2δ。如果要求H很短,则需要留适当余量增加H,折弯后再切断添加的金属。
- 弯曲有孔的零件时,为了避免孔的变形。
- 金属冲压件的形状应简单对称,深度不宜过大。以尽量减少拉深次数,便于成型。
- 金属冲压件的圆角半径不增加加工工序。否则会增加拉深次数,模具数量也会增加,容易产生废品,增加成本。
用于金属冲压件的模具采用弹簧压型卸荷板还是固定卸荷板,主要取决于卸荷力的大小,而材料厚度是主要考虑的因素。随着模具所用弹性元件弹力的加强(如采用矩形弹簧),弹性压力卸荷板的卸荷力大大增强。
根据目前的情况,当物料厚度小于2mm时,使用弹簧压力脱料器比较实用,当大于2mm时,使用固定脱料器比较实用。模具冲裁的材料厚度为1mm,可采用弹簧加载卸料板。
金属冲压件是通过压力机和模具对板材、带材、管材、型材等施加外力,使其产生塑性变形或分离,以获得所需形状和尺寸的工件(冲压件)而形成的。
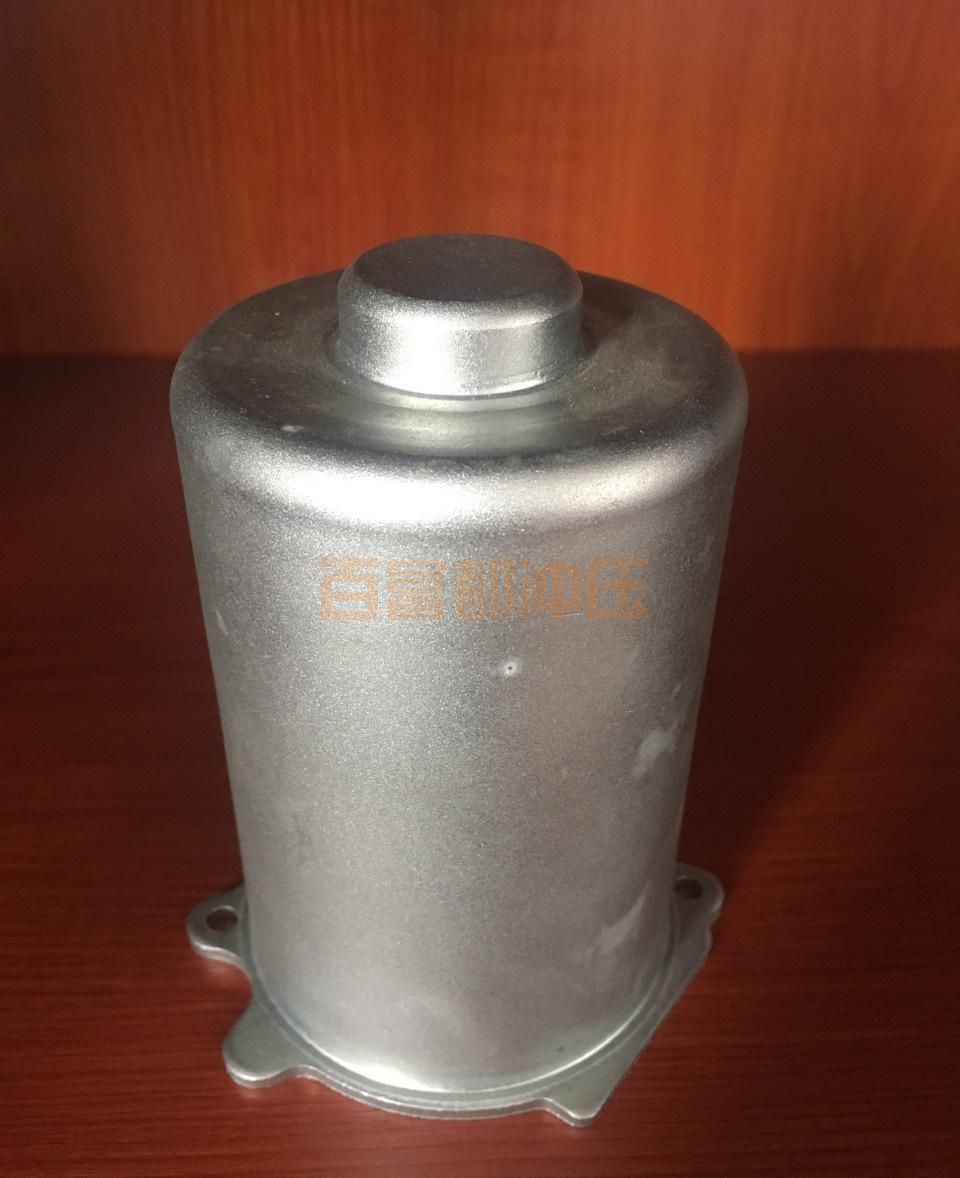
金属冲压模具的外观和精度要求。
五金冲压模具的装配适合于集中装配,在装配过程中经常采用修复法和调整装配法,以保证装配精度。这样,就可以利用精度不高的零件达到较高的装配精度,降低零件的加工要求。五金冲压模具装配的技术要求有以下几个方面:。
- 冲压模具外观技术要求:
- 每个模板的边缘和装配后的冲压模具的外露部分应该是倒角或圆形,小到有毛刺和锐角。每一外观表面不得有严重的划痕、瘀伤或粘性污垢。也不应有刺绣痕迹或部分未经加工的粗糙表面。
- 根据冲模的工作状态,应在冲模适当平衡的位置安装一个吊环或吊环。多分型面冲压模具应采用锁紧板锁紧,以防止动模板在运输过程中因振动而损坏。
- 整体尺寸,关闭高度,安装和定位尺寸,弹射方法,模具开启行程等。冲压模具的设计应满足设计图纸的要求,并应与所用设备的参数合理匹配。
- 冲压模具应有标记号,每个模板应印有加工和装配基准角度的顺序号和印记。
- 冲压模具的动模、定模的连接螺钉必须拧紧、牢固,其头部不应高出模板的平面。
- 冲压模具外观上的各种辅助机构,如吊钩、摆杆、锁、冷却水喷嘴、限制开模顺序的液压和电气元件等,其安装应完整、规范、可靠。
- 为了保证冲压模具及其成形冲压件的质量,冲压模具的装配应具有以下精度要求:。
- 冲压模具零件应满足一定的相互位置精度如同轴度、平行度、垂直度、倾斜度等。
- 运动部件要有相对运动精度要求,如各种机构的回转精度、回转运动精度和直线运动精度。
- 导向定位精度:如动模、定模的开合运动导向,上模和下模,型腔(凹模)和型芯(凸模)的安装定位,以及滑动运动的导向定位等。
- 装配精度和接触精度:装配精度主要是指零件表面相互配合时所应达到的配合间隙或干涉程度。如型腔与型芯、镶件与模板孔的配合,导柱与导套的配合,以及与模板的配合等。接触精度是指两个配合和连接面达到规定的接触面积大小和实际接触点的分布程度。如分型面接触点的均匀性、锁楔坡度的接触积大小等。
- 其他方面的精度要求:如冲压模具装配过程中的紧力、变形、润滑和密封等。以及冲压模具工作时的振动、噪声、温升和摩擦等控制,应满足冲压模具的工作要求。