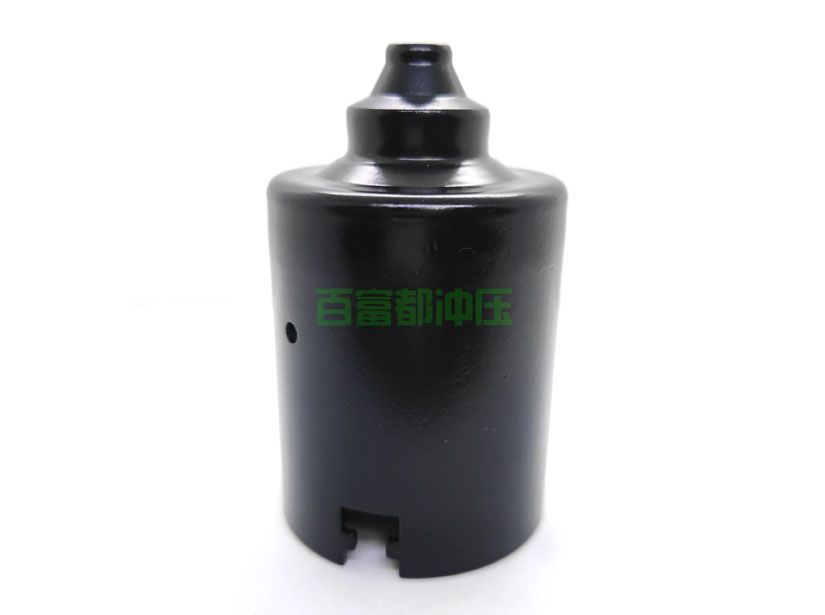
在冲压加工过程中,特别是冲孔加工过程中,我们经常会遇到冲头断针的现象。出现这类问题时,我们往往直接更换新的冲床针,但不能从根本上解决冲床针断裂的问题。下面我们分析一下冲压过程中冲头断针的常见原因及解决方法:。
1) 产生的废料堵塞了下模。
解决方法:重新修改下料孔,使废料能够顺利落下。
2) 冲针的固定部分(夹板)和导向部分。
解决方法:修复或重新将线切割成块,使冲头针可以平稳地上下移动(脱料板)被偏移。
(3)冲模关闭高度设定过低,导致冲头进入下模时间过长。
解决方法:调整冲头的闭合高度,使冲头针适当地进入下模。
4) 脱料板设计不合理,造成冲针受力不均匀。
解决办法:重新设计脱料板与冲头之间的间隙。
5) 冲针刀片设计太短,操作过程中与脱料板发生碰撞。
解决方法:重新选择合适的冲针,或增加刀口的长度。
6)冲针表面有应变、划痕,卸料时冲针受力不均匀。
解决办法:用新的打孔针替换。
打孔针。
7) 冲针边缘磨损、钝。
解决方法:重新打磨打孔针边缘。
8) 选择的冲针太细、太长或不够结实。
解决办法:需要重新选择其他冲针类型。
9) 冲针的硬度不合适,选择的冲针材质不合适。
解决办法:更换适当的冲头针材料,或进行热处理。
10) 模具定位装置设计不合理,造成冲针只冲向一侧,造成冲针受力不均。
解决方法:调整模具定位装置,使冲针在冲裁时能切割完整的材料。
11) 冲针固定不牢,在冲针过程中晃动。
解决方法:重新固定冲头,使其不能上下移动。