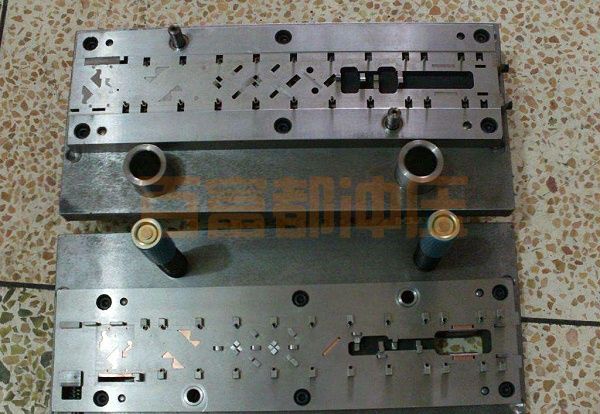
冲压模具凸模、凹模刃口大小精度及公差对金属冲压件制品尺寸精度有影响,另外冲压模具间隙是否合理与此有关。 所以在生产过程中对这些问题必须引起重视。下面我们来谈谈这方面的内容。1.什么是凸模?它有哪些特点?2.什么是凹模呢?它有哪几个特点?3.它们之间有何区别?又如何比较?4。怎么判断?怎样测量?等等。 在进行冲压加工时,需要弄明白凸模与凹模刃口的大小,否则就会弄得很不理想,那么下面我们来看看。 一、冲裁件的锥度用光亮带来测量:在测量与使用过程中落料件的锥度时,先将光亮带套到冲孔件上,然后再把光亮带以小端尺寸套到落料件上,最后再测量出凹模尺寸,即得到冲孔件的凸模尺寸; 落料件的大端尺寸大于冲孔孔径,小于小端尺寸; 模具使用时,其凸模刃口尺寸将越用越小,凹模刃口尺寸也将越用越大,造成凸模与凹模间隙不断增大,直到尺寸超差而无法继续使用。
计算原则:
设计落料模时,首先要确定凹模的刃口大小:凹模作为基准,缝隙取凸模处,也就是冲裁缝隙是靠缩小凸模的刃口而获得的。
设计冲孔模前,首先要确定凸模刃口直径和凸模与凹模之间的冲裁间隙大小。
冲模的磨损规律是由落料模到凹模再到工件,zo=(?);冲孔模比凸模更易磨损,且工件孔越大,zo越大; 冲裁成形工艺参数对模具磨损影响较大;合理选择工作带长度和压边力有助于提高生产率和降低能耗;适当增加凹模型腔深度可以有效地减少磨损面积;减小冲压力有利于降低材料消耗;改善润滑条件可大大降低摩擦系数;缩短生产周期;降低成本;提高效率;节约时间。 模具磨损预留量要与工件制造精度相适应;
冲裁间隙应控制在一定范围内,一般不超过zo=?
模具刃口对冲压件精度影响很大,因此在保证模具精度的前提下,应尽量减小冲压件的间隙值。 根据我们多年来的生产实践体会,选择合适的加工方法和工艺参数是提高零件质量、降低加工成本的重要手段之一。1.确定合理的切削深度。这是决定冲压件表面质量优劣的关键。正确地选取切削用量尤为重要。计算好刀具角度。适当增加前角;增大前倾角。减小后角。 冲模精度对工件精度影响较大,一般为2~4级。
其特点是:结构简单,使用方便;
对于形状复杂的刃口制造偏差应取工件相应部位公差值中的1/4;
形状简单的刃口尺寸则可按其相应部位的制造偏差值的1/8来选取。
对于工件尺寸公差有变化的情况下,可将冲模刃口处的制造偏差用“入体”表示为单向公差;对已加工好或有一定精度要求的零件来说,其几何形状误差和位置公差可以用一个统一公式表示:式中:X——被测量;Y——测量点到基准轴线距离;Z——量具中心距;零件图如图1所示。均为数值。是绝对数字。没有相对数。但对磨损后没有改变的尺寸通常标有双向偏差。落料件的上下偏差均为0, 0, 0,冲孔件的上下偏差都为0, 0。